В этой статье мы подробно рассмотрим холодную высадку и холодную штамповку.
В статье будут более подробно рассмотрены такие темы , как:
- Принцип холодной высадки
- Типы холодной высадки или процессов холодной штамповки
- Применение и преимущества холодной штамповки
- И многое другое…
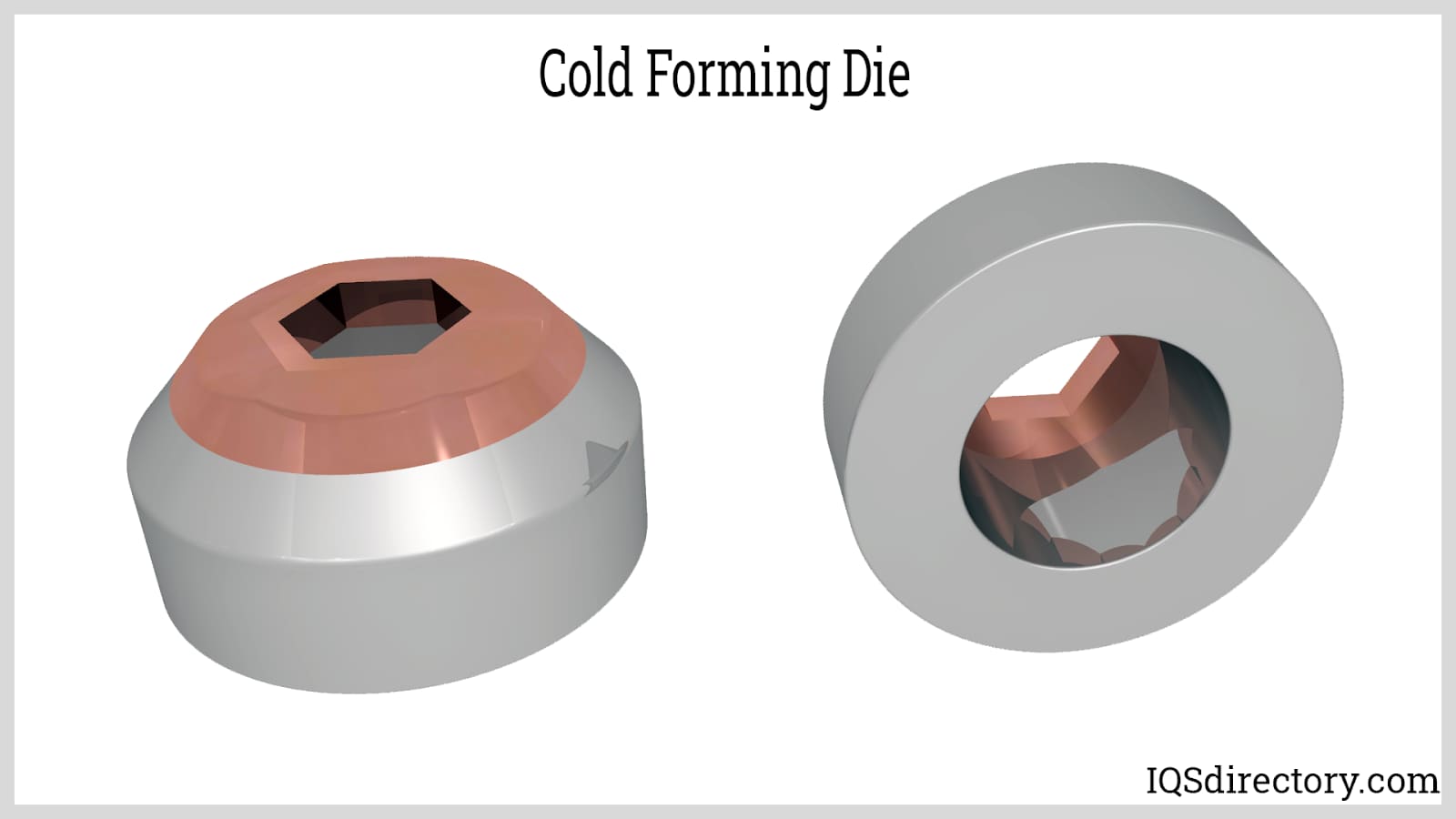
Глава 1: Принцип холодной штамповки
В этой главе будут рассмотрены определение, материалы и методы оснастки, используемые при холодной штамповке.
Что такое холодная высадка?
Холодную высадку также называют холодной штамповкой, что делает эти термины взаимозаменяемыми. Холодную высадку или формование можно определить как процесс непрерывного придания определенной формы или дизайна металлической проволоке без добавления тепла. Этому способствуют высокоскоростные молотки, матрицы и пуансоны.
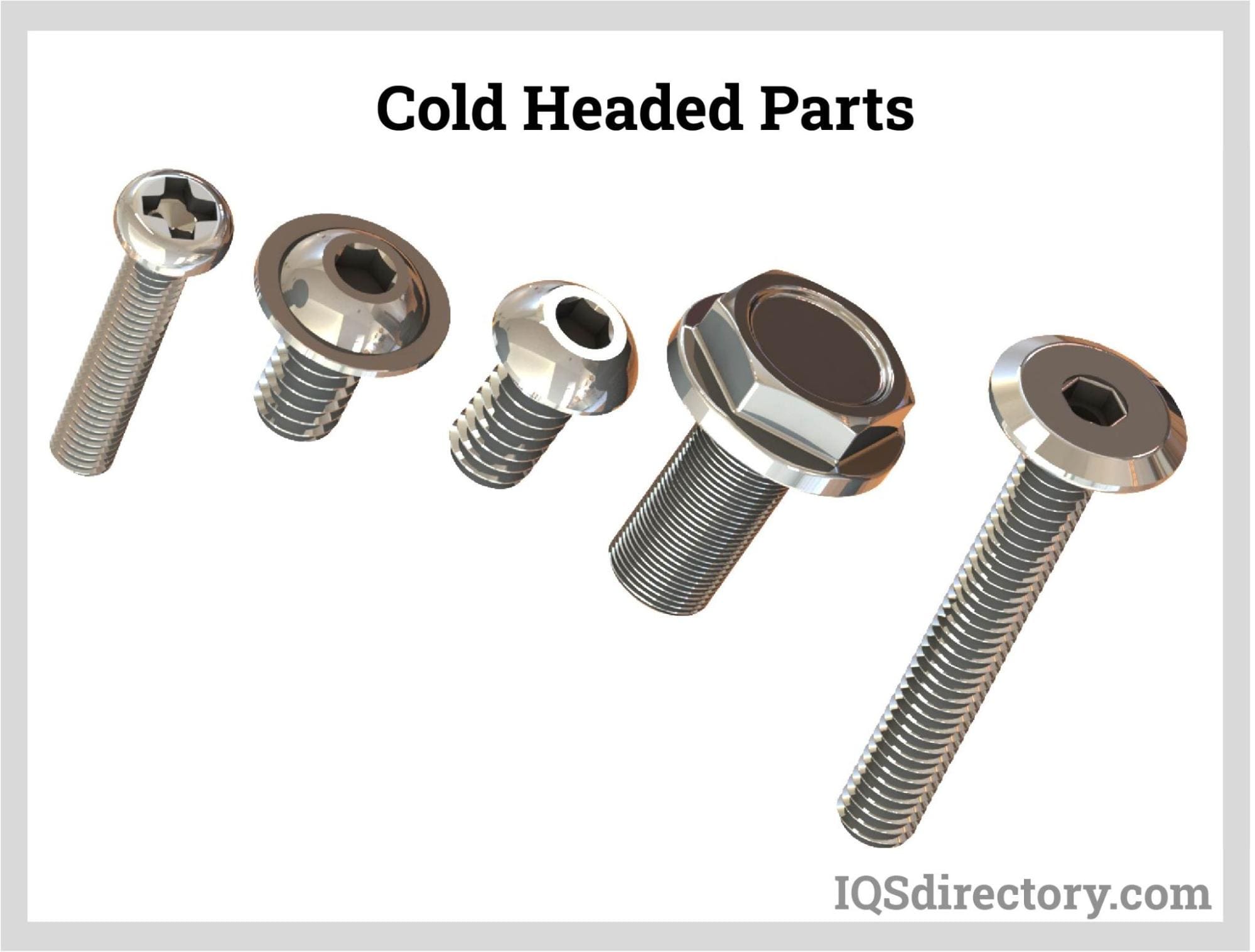
Холодная штамповка начинается с заготовки, вырезанной из прогрессивного мотка или проволоки; затем машина холодной высадки использует цепочку из прочных молотков и матриц для формирования детали. Холодная высадка также может быть определена как процесс приложения усилия от пуансона к торцу металлической заготовки в матрице. Усилие должно превышать предел упругости металла или предел текучести, чтобы обеспечить пластическую текучесть.
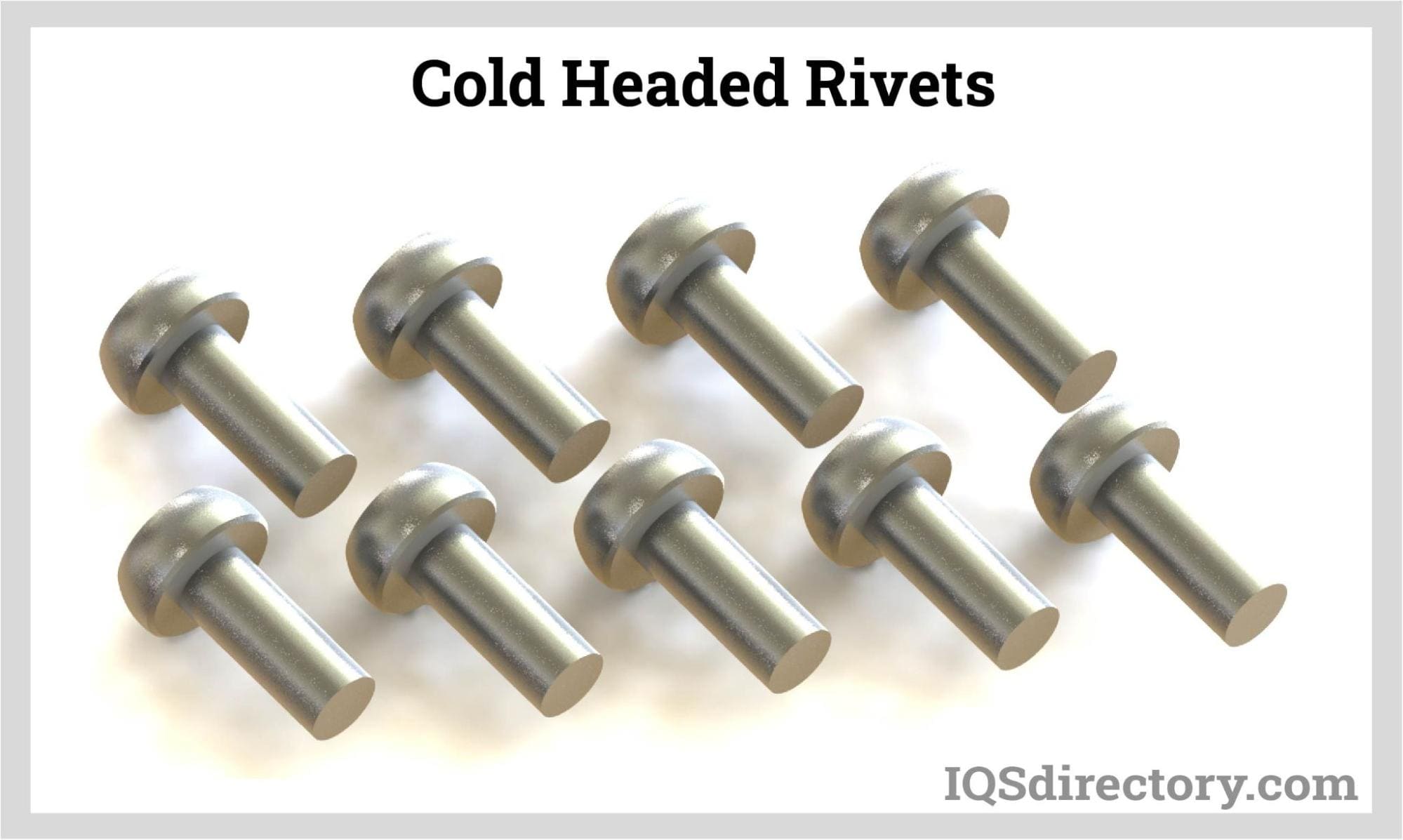
Холодную высадку можно рассматривать как операцию ковки без использования тепла. Это выполняется вместе с другими процессами холодной высадки, такими как прокатка заготовок, прошивка, заострение, накатывание резьбы, калибровка и обрезка. Холодная высадка — это также промышленный процесс, который служит основным способом изготовления металлических фитингов с резьбой и крепежных деталей.
Процесс холодной высадки включает ковку на очень высоких скоростях, при которой спиральная проволока аккуратно обрезается по длине при комнатной температуре и надлежащем давлении. Затем он перемещается через непрерывную матрицу и отверстия инструмента для перемещения обрабатываемого металла и придания ему формы для получения требуемого изделия. Процесс холодной высадки может уменьшать или увеличивать диаметр и длину исходного материала, а также может удалять небольшие количества материала путем прошивки и обрезки. Все процессы и операции холодной высадки выполняются в непрерывном плановом режиме.
Исторически холодная высадка использовалась только для изготовления очень простых крепежных изделий. В настоящее время холодная высадка представляет собой автоматизированный высокоскоростной многостанционный метод, позволяющий экономично производить композитные крепежные изделия и другие компоненты. С совершенствованием технологий и ростом объемов холодной высадки оборудование позволяет выполнять холодную формовку деталей из более прочных металлов, включая жаропрочные сплавы и нержавеющую сталь.
Материалы и инструменты, используемые при холодной штамповке
Все холодные жатки имеют определенный метод отрезания и отмеривания куска катушки проволоки. Способ помещения проволоки внутрь холодной жатки и ее отрезания часто варьируется в зависимости от необходимой марки. После того, как проволока окажется внутри машины, останется только отрезной нож. Этот нож ударяет по проволоке в определенном направлении, отрезая отдельный кусок. Этот процесс часто состоит из множества частей, не говоря уже о отрезном ноже.
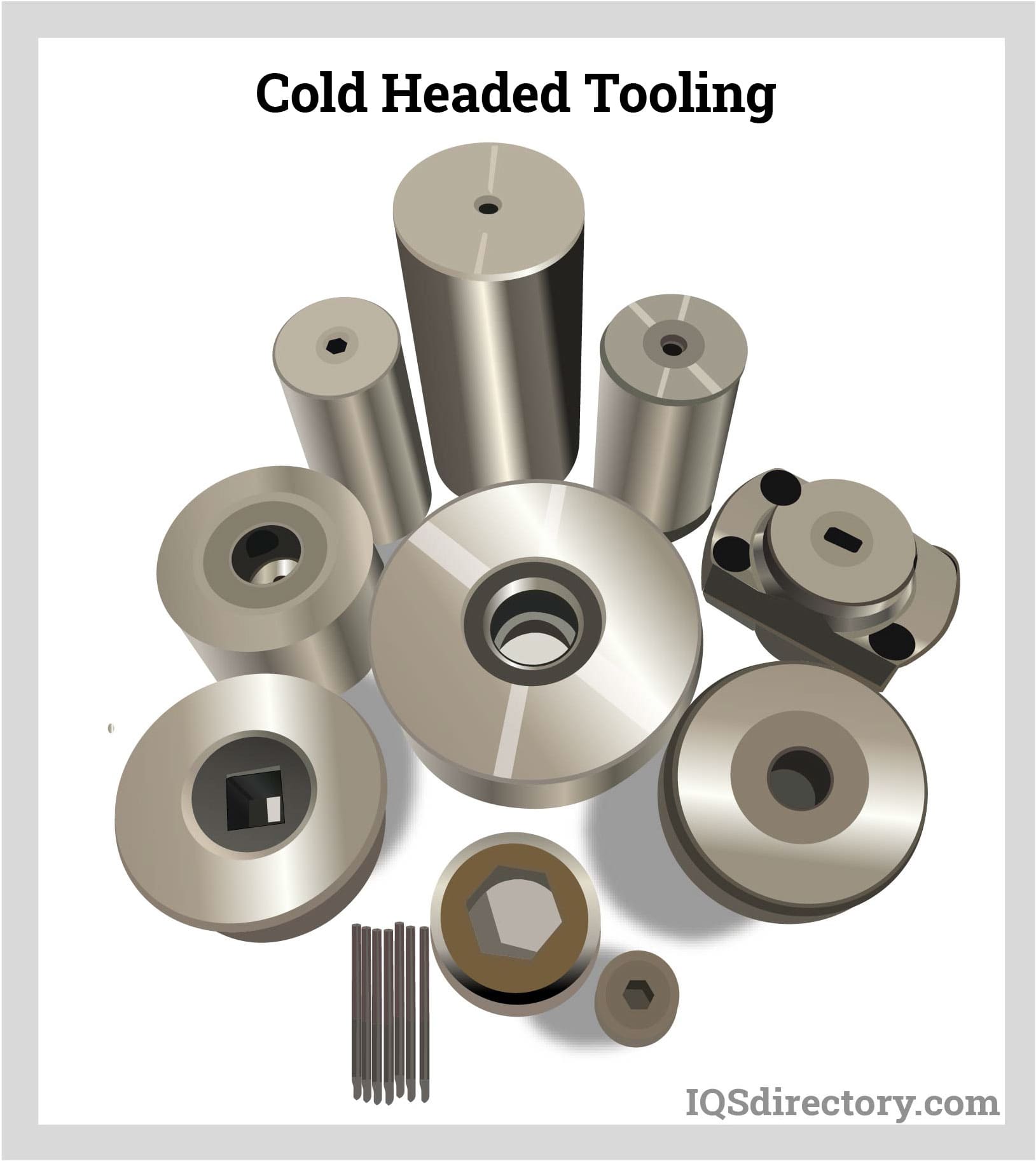
Штампы для холодной штамповки
Поскольку матрицы должны выдерживать более высокие нагрузки, они очень большие по сравнению с пуансонами. Матрицы находятся на стационарной части холодной жатки. Каждая матрица обычно состоит из нескольких частей. Рабочий инструмент часто изготавливается из трех-четырех различных сегментов, которые образуют всю рабочую часть матрицы. После этого все они помещаются под сильным давлением в большую круглую емкость, обычно называемую кожухом.
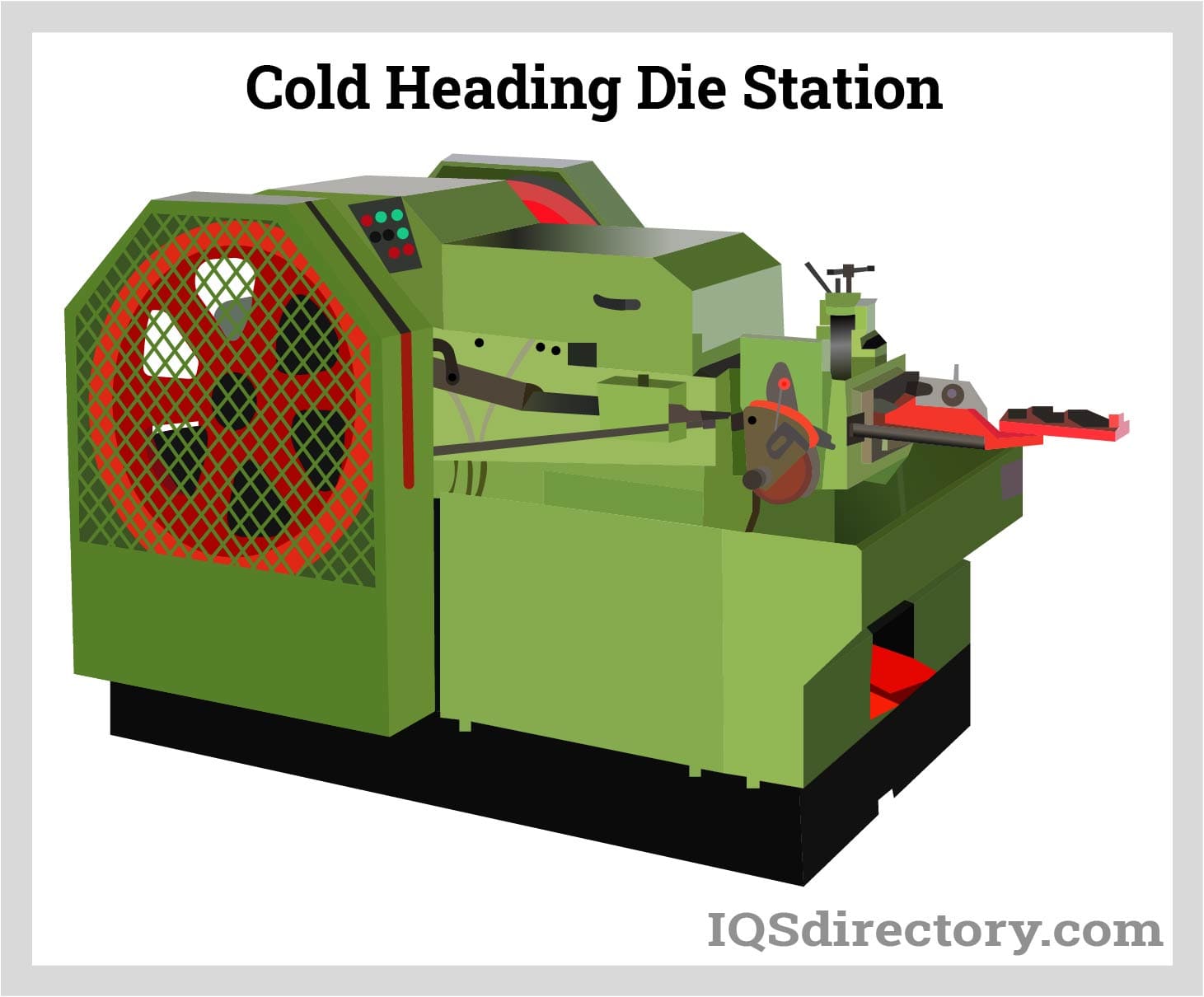
Вставляемая часть матрицы подвергается сильному радиальному давлению при каждом ударе. Они быстро взорвутся и выйдут из строя, если у них нет какой-либо опоры. Для решения этой проблемы их с усилием вдавливают в корпус. Этот корпус намного больше и способен поглощать и рассеивать все нарастающее давление, обеспечивая целостность матрицы для многих деталей или циклов.Эти корпуса штампов можно использовать много раз, прежде чем их потребуется заменить.
Все эти штампы имеют отверстие определенного размера в центре оси инструмента, на котором устанавливается деталь. Из-за высокого давления, оказываемого на детали, что мешает им вылетать через матрицу и выходить через заднюю стенку станка? Затем включается система выбивных штифтов. Цепочка штифтов установлена в задней части матрицы для выполнения двух функций. Первоначально во время обрабатывающей части хода они препятствуют выталкиванию детали через заднюю часть матрицы. Во-вторых, на последней фазе процесса формования эти штифты отливают вперед, выталкивая деталь из матрицы.
Пуансоны для холодной штамповки
Пуансоны находятся на подвижной части станка. По сравнению с матрицами пуансоны меньше, потому что они подвергаются меньшему давлению в процессе высадки. Пуансоны также подвергаются большой нагрузке и должны содержаться в корпусах пуансонов.
Эти пуансоны определяют форму или конструкцию головки для шурупов. Один пуансон будет первым ударом, а другой — последним. Пуансоны также могут служить опорой для штифта, который проталкивает деталь внутрь матрицы. Обычно это происходит в тех случаях, когда штампы помогают запертым экструдерам или выемчатым штифтам, которые помогают обратному выдавливанию образовывать выемки в деталях.
Передача холодной штамповки
Это последняя инструментальная система в передаточном механизме. Передача холодной штамповки намного проще, когда используется машина с одной матрицей и двумя выдувными машинами, потому что требуется только одна передача, которая представляет собой срез матрицы. Тем не менее, как только процесс ускоряется до нескольких штампов в многопластовой жатке, механизм перемещения становится важным компонентом.
Наиболее распространенными инструментами, используемыми для передачи, являются пальцы или захваты, которые удерживают детали при перемещении от одной матрицы к другой. Пальцы часто изготавливаются на заказ с учетом желаемых потребностей каждой детали. Геометрия детали важна при перемещении детали, поскольку детали могут быть очень тяжелыми. Возможно смещение головки, а иногда и большого выступа, что приведет к провисанию детали при ее извлечении из матрицы.
Человек, работающий с фильерой, должен убедиться, что время перемещения выбрано правильно для удержания и захвата детали до того, как она полностью выйдет из матрицы. Однако при перемещении деталь не перемещается до тех пор, пока она полностью не выйдет из матрицы. Этот процесс требует большой практики и опыта от специалиста по наладке, чтобы овладеть мастерством.
Машины, используемые для холодной высадки
Машины для холодной высадки превращают металлическую заготовку в детали идеальной формы с использованием возвратно-поступательного действия, который вдавливает молоток в предварительно отформованный штамп. Машина холодной высадки известна как штамповочная машина в механической обработке и производстве. Если исходное сырье не меняется, материалы изготавливаются по желанию заказчика.
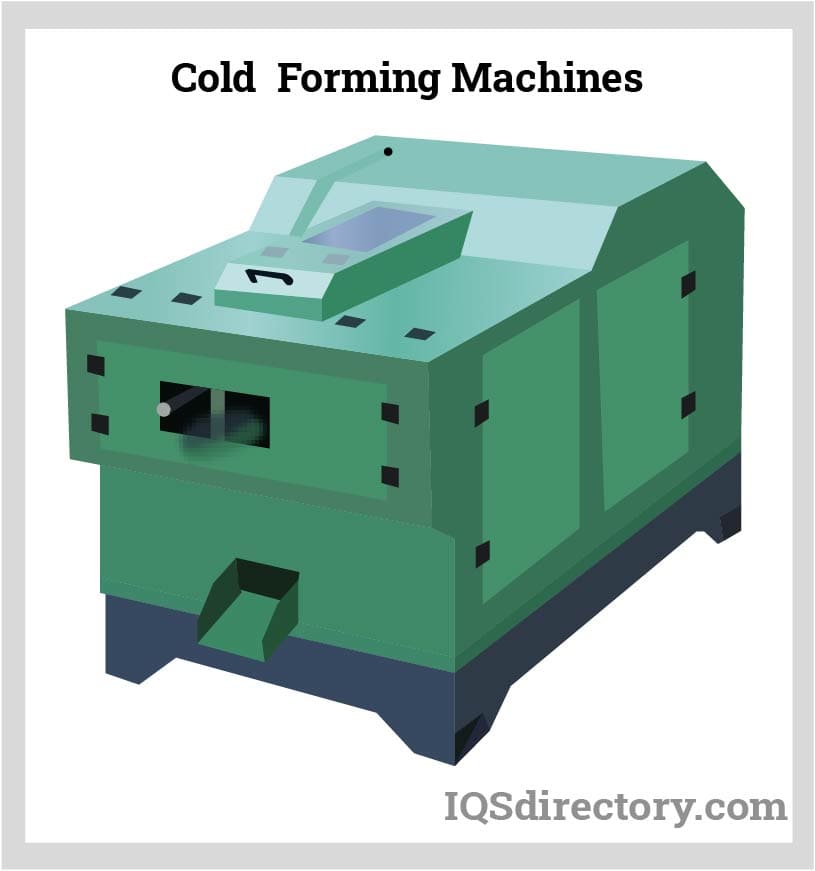
В машине для холодной штамповки конические шестерни соединяются в пары и надеваются на один конец коленчатого вала. Вал с приводной конической шестерней надевается на кулачковую шестерню, а ползунок ножниц вертикально надевается на вал ролика, состоящий из ведомого ролика кулачкового объекта или устройства. Полезная модель устраняет все встречающиеся недостатки известного уровня техники, а также коэффициент трения при движении. Сила удара между всеми компонентами режущего и подающего механизмов очень мала по величине. Бесперебойная работа оборудования в значительной степени сводит к минимуму рабочий шум и повышает производительность и качество продукции.
Операция холодной высадки
В процессе холодной высадки используются высокоскоростные автоматические формовочные машины или холодные жатки. Это оборудование способно превращать простую проволоку в деталь сложной конструкции с очень жесткими и повторяющимися допусками за счет использования метода обработки со скоростью 400 заготовок в минуту. Проволока определенной длины помещается в матрицу, а затем молотком выдавливается или деформируется материал, придавая ему требуемую форму.
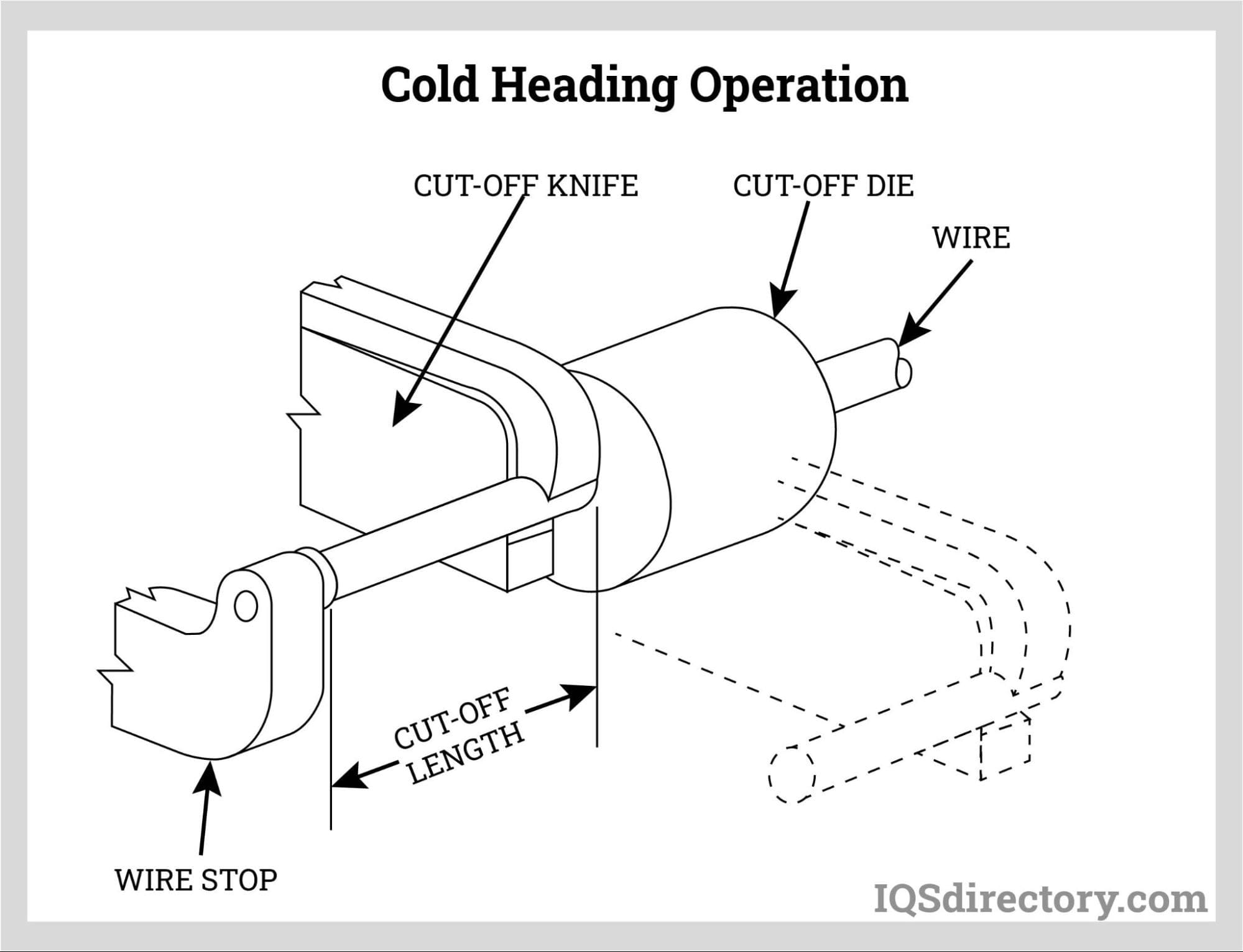
Поскольку процесс холодной высадки зависит от объема, а также использует определенный объем для изготовления конечной детали сложной формы точно такого же объема, материал будет просто переставлен. Потери лома или материала очень низкие.
Последние разработки в области оборудования для холодной штамповки
Оборудование для холодной высадки и холодной штамповки в последнее время стало намного более совершенным. В настоящее время изготавливаются станки с пятью или более штампами и множеством функций, позволяющих максимально увеличить производство как коротких, так и длинномерных деталей. Одной регулировкой можно изменить ход подачи, функции фрезерования, выталкивания и синхронизации передачи. Система управления с ЧПУ предоставляет оператору быстрый доступ к необходимым производственным данным. Мгновенные настройки замены работают как для компонентов матрицы, так и для пуансона, которые настраиваются в автономном режиме, что позволяет максимально сократить время производства. Также могут использоваться многопозиционные жатки.
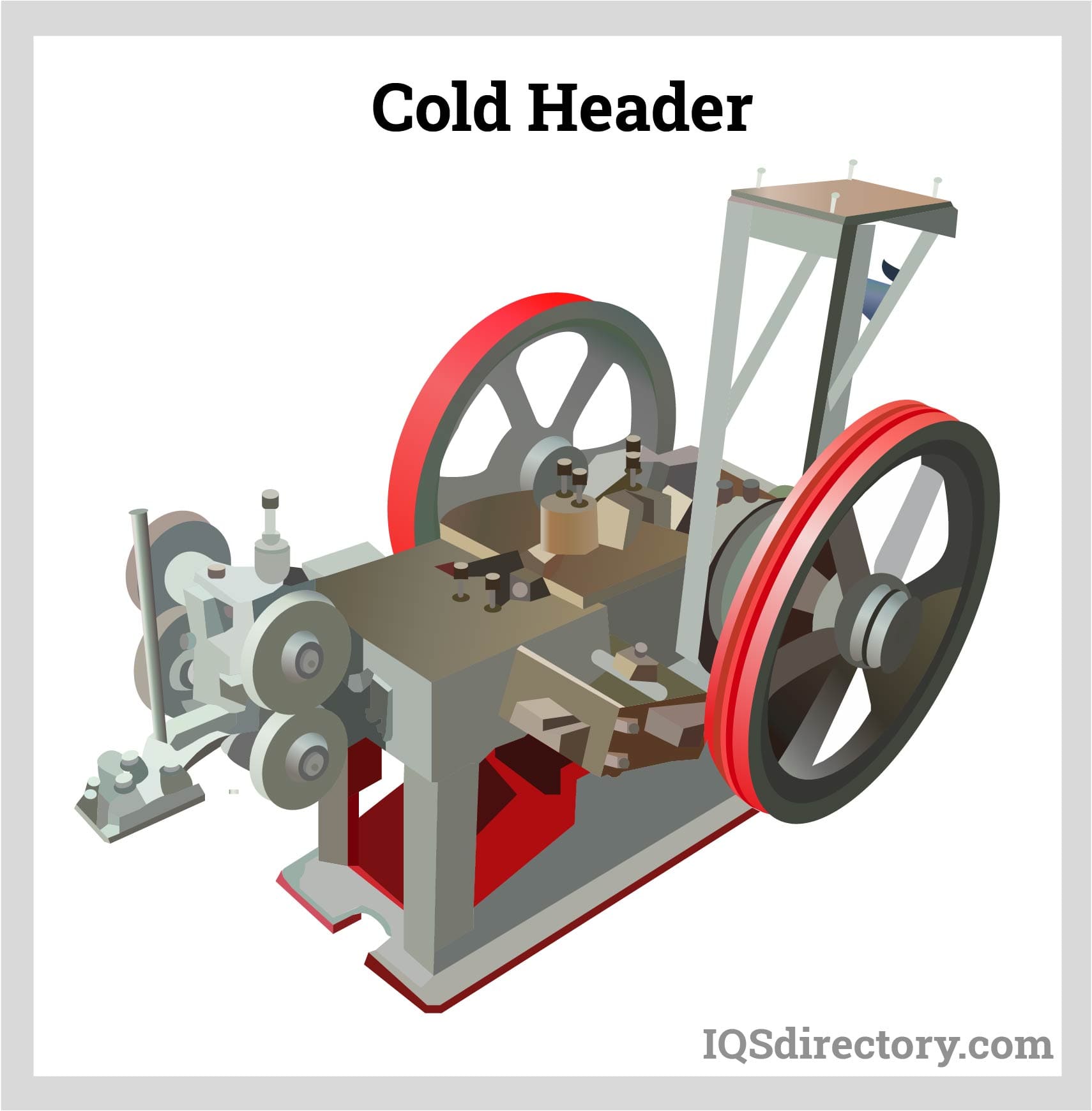
Они выполняют комбинацию операций выдавливания, осадки и других операций холодной штамповки. Операции холодной штамповки также значительно увеличили возможности и скорость производства высадки. Расширенная информация и знания в области металлургии позволили производить высадку и холодную штамповку гораздо более твердых материалов. Ведущие производители сплавов тщательно контролируют анализ и производство марок, чтобы удовлетворить требования к большей прочности и коррозионной стойкости детали с насадкой.
Возможно изготовление определенных марок AISI в пределах контролируемых границ анализа для улучшения способности к холодной формовке там, где требуются хорошие качества холодной высадки, более высокая производительность и последующая обработка второго порядка. В некоторых случаях анализ процесса холодной штамповки позволяет более экономично изготавливать крепежные детали определенной формы. Более прочная инструментальная сталь увеличивает срок службы штампов. Производители изделий с холодной высадкой производят сплавы, которые достаточно универсальны для изготовления как механической обработкой, так и высадкой.
Глава 2: Типы холодной высадки
Типы оборудования для холодной высадки
Существует два основных типа оборудования, используемого при холодной высадке, а именно:
- Формовщики деталей
- Холодные высадки
В обоих типах используются горизонтальные плунжеры возвратно-поступательного движения и неподвижные опоры. Оборудование для холодной высадки может включать от одной до семи последовательно расположенных матриц с различными размерами среза. Ассортимент холодной высадки, который может предоставить производитель, во многом зависит от количества имеющихся в его распоряжении станков.
Двумя основными компонентами процесса холодной высадки являются штампы и пуансоны. Пуансоны передают необходимое усилие от станка к материалу и обеспечивают тщательный контроль размеров деталей внутри. Штампы направляют материал и придают ему желаемую форму и геометрические размеры.
Типы процессов холодной высадки
Холодная высадка получила свое название от процесса осадки.
Осадка холодной высадкой
Это метод, используемый для изготовления головки на болте или шурупе. Осадку можно определить как процесс, при котором материалы объединяются в единое целое на детали, такой как хомут или головка. Другими словами, в областях, подвергаемых деформированию, диаметр все больше увеличивается. Используя язык холодной высадки, производители говорят «максимальное количество диаметров, которые могут быть деформированы».
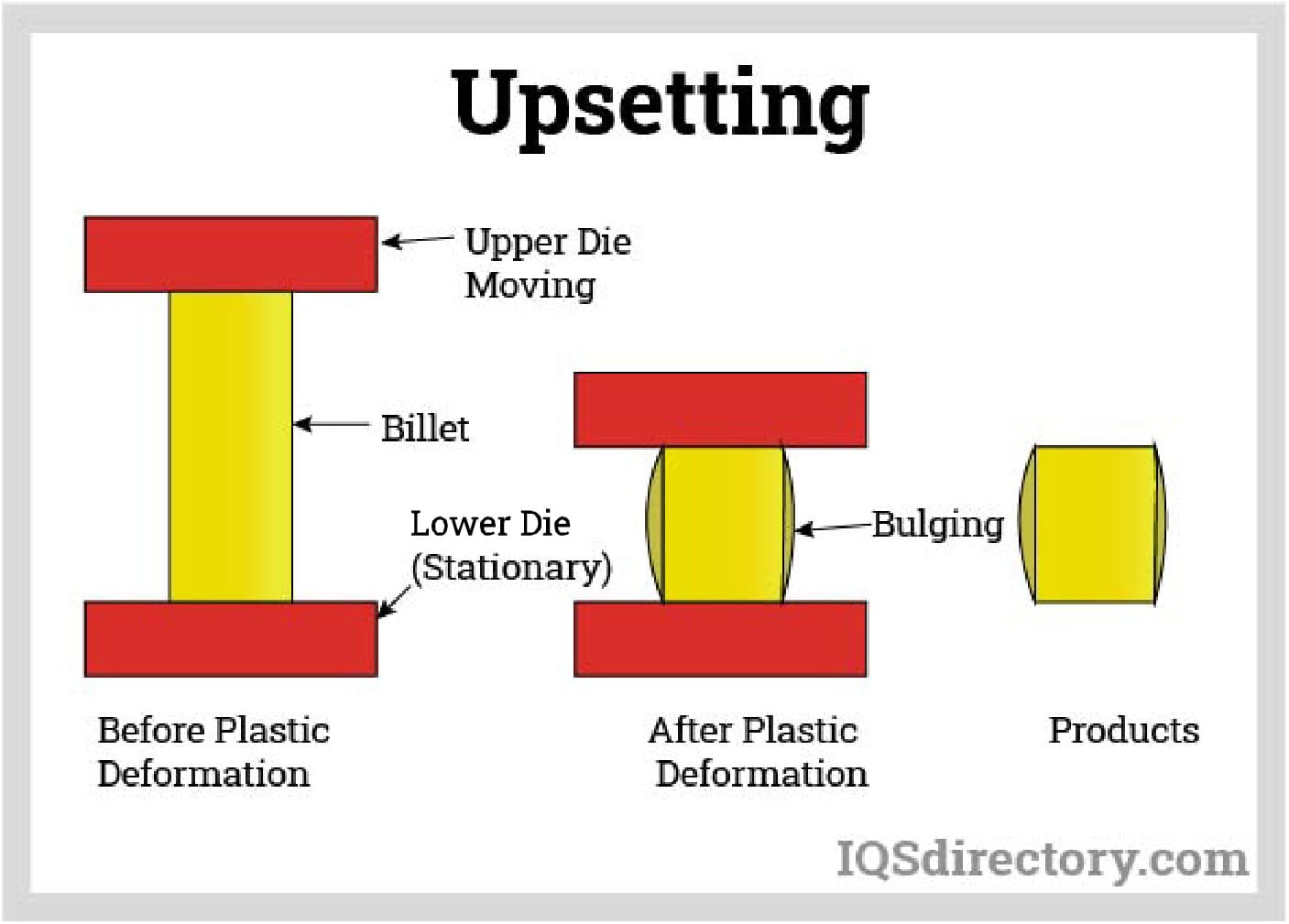
Хотя это выглядит и звучит намного сложнее, осадка — более простой способ формования. Это простой цилиндр, который вырезается или снимается с длинномерной катушки непрерывной проволоки, помещаемой внутрь машины. Для деталей, которые станут болтами и шурупами, или деталей с наружной резьбой, цилиндр намного длиннее своего диаметра. Цилиндр можно разбить на различные секции, где каждая секция имеет одинаковый диаметр и высоту. Каждая секция называется диаметром. Некоторые детали очень длинные и тонкие, такие как винты и болты, причем каждый начальный отрезок проволоки состоит из секций разного диаметра.

За годы работы инженеры усвоили, что за один раз можно переместить или сжать только ограниченную часть материала, прежде чем он лопнет или треснет. В условиях холодной высадки ограничение составляет примерно два процента диаметров за каждый удар. Многие головки болтов или шурупов имеют внутри материал более двух диаметров, поэтому для получения требуемого конечного результата по ним необходимо ударить несколько раз.
Существует ограничение на то, сколько материала можно подвергнуть осадке за один удар в контролируемых условиях. Формирование сложной детали, в которой много металла вдавливается дальше, лучше выполнять в два этапа, или ударами. Именно по этой причине обычно используются однотактные и двухтактные насадки. Осадки обычно рассчитываются исходя из диаметров проволоки. Затем общая длина металлической заготовки делится на диаметр проволоки.
Таким образом, например, берем 5-дюймовую металлическую заготовку из проволоки 1/2 дюйма, длина которой равна десяти диаметрам. Для каждого выдува на сплошной штамповой жатке наибольший размер проволоки, который может быть подвергнут контролю за опрокидыванием, приблизительно равен 2 1/4 диаметра. Для изготовления требуемой крепежной головки можно использовать примерно 1 » из 5″ металлической заготовки. Однако большинство высадок с одним выдувом имеют диаметр от 1 до 1 1/4 дюйма.
По линии высадки с двумя выдувами можно подвергать осадке изделия диаметром до 4 1/2 дюйма. На начальной стадии контакта металлической заготовки с пуансоном часть заготовки, которую необходимо опрокинуть, выступает из матрицы без опоры. Если эта длина остается без опоры или превышает 2 1/4 в диаметре, металлическая заготовка прогнется сама по себе при ударе, создавая дефект холодного прессования. Если будет предпринята попытка опрокинуть 3 дюйма, возможно, это будет невозможно контролировать, поскольку это равно шести диаметрам.
Однако здесь, конечно, есть несколько ожидаемых исключений из эмпирического правила. Очень сложная жатка и скользящий пуансон, который поддерживает большую часть металлической заготовки, позволяют производить два выдува диаметром 6 1/2 дюйма. Учитывая многопозиционные жатки, общее количество диаметров, которые могут подвергаться осадке, ограничено только количеством доступных штампов. Взаимосвязь диаметра проволоки и процесса осадки имеет решающее значение. Неправильный расчет может привести к несоответствию диаметра проволоки возможностям станка.
Экструзия холодной высадкой
В холодной высадке термин «экструзия» является общим термином. Это связано с тем, что существуют три совершенно разных типа процессов экструзии. Существует два типа прямой экструзии: экструзия с захватом и открытая экструзия. При этом материалы выталкиваются перед инструментом (вперед). Другой тип выдавливания — обратное выдавливание. При этом материал подается назад против направления движения инструмента.
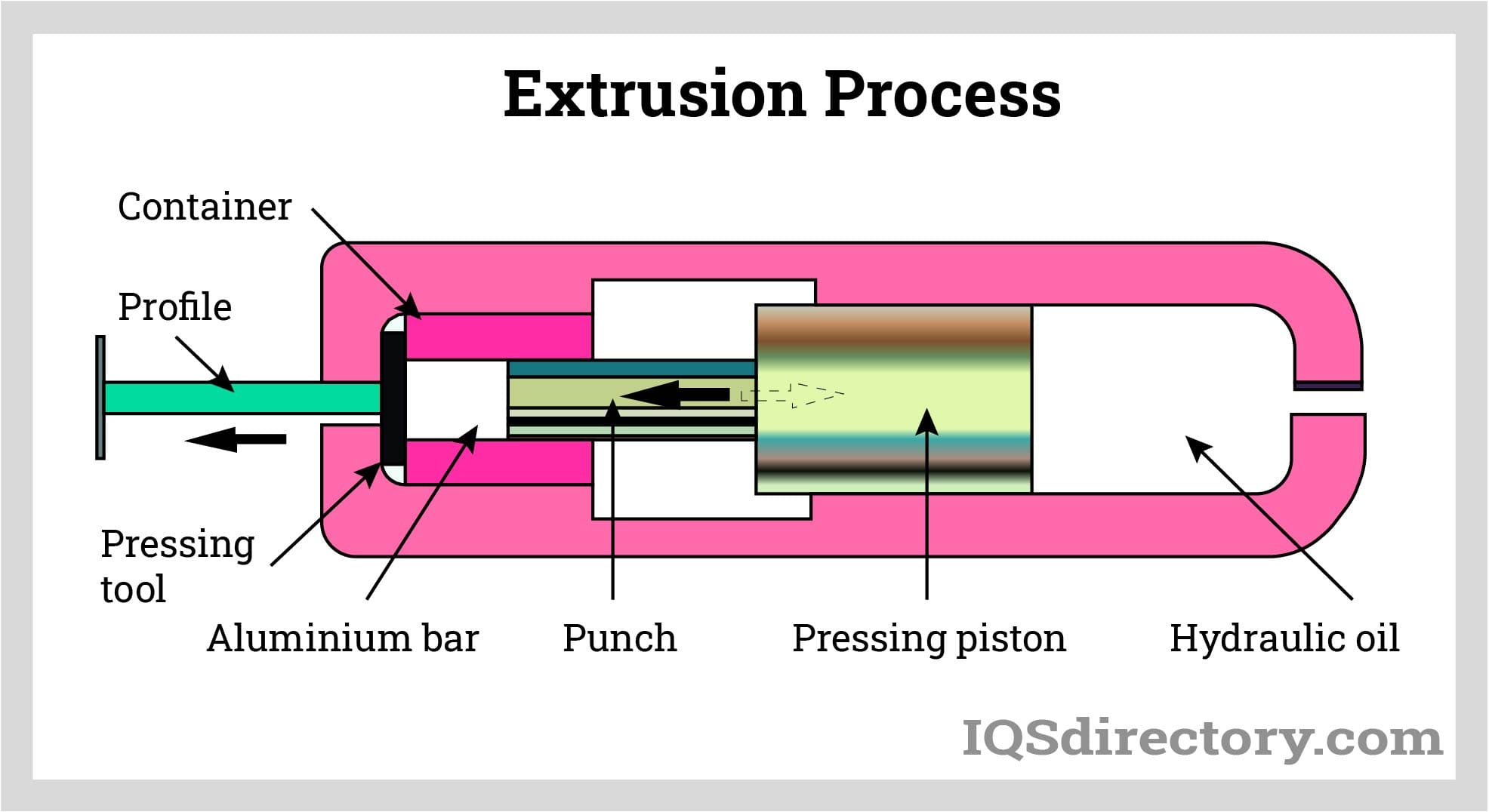
Например, прямое выдавливание в основном происходит, когда заготовка подается в матрицу диаметром намного меньшим, чем она сама. Длина увеличивается, а диаметр уменьшается. С другой стороны, процесс обратной экструзии включает в себя воздействие на металлическую заготовку высокого давления от углового пуансона. Поскольку металлической заготовке больше некуда идти, она разбрызгивается вдоль внешней границы пуансона, а затем течет в обратном направлении.
Процесс прямой экструзии используется для изготовления винтов, ступенчатых валов или болтов, в то время как процесс обратной экструзии используется для изготовления многочисленных цилиндрических конструкций и форм, таких как втулки, гайки и заклепки. Экструзия, как и осадка, изменяет форму металлической заготовки; следовательно, потери используемого материала минимальны. Процесс экструзии может быть как открытым, так и замкнутым.
Открытая экструзия означает, что заготовка вдавливается в матрицу, в то время как процесс принудительной экструзии заключается в том, что заготовка полностью помещается в матрицу. Контролируемые процессы осадки зависят от диаметров проволоки, а процессы выдавливания основаны на уменьшении площади заготовки. Обычно это рассчитывается в процентах и зависит от угла выдавливания.
Основное правило открытой экструзии заключается в том, что процент уменьшения площади за один удар не должен превышать 30 процентов. Всегда имейте в виду, что измерения диаметра, выполненные до и после экструзии, не используются для прямого расчета уменьшения площади.
Открытая экструзия
Открытая экструзия не ограничивает деталь инструментами. Это позволяет расположить экструзионную часть инструмента близко к верхней стороне матрицы. Это позволяет максимально увеличить длину детали, которую можно экструдировать.
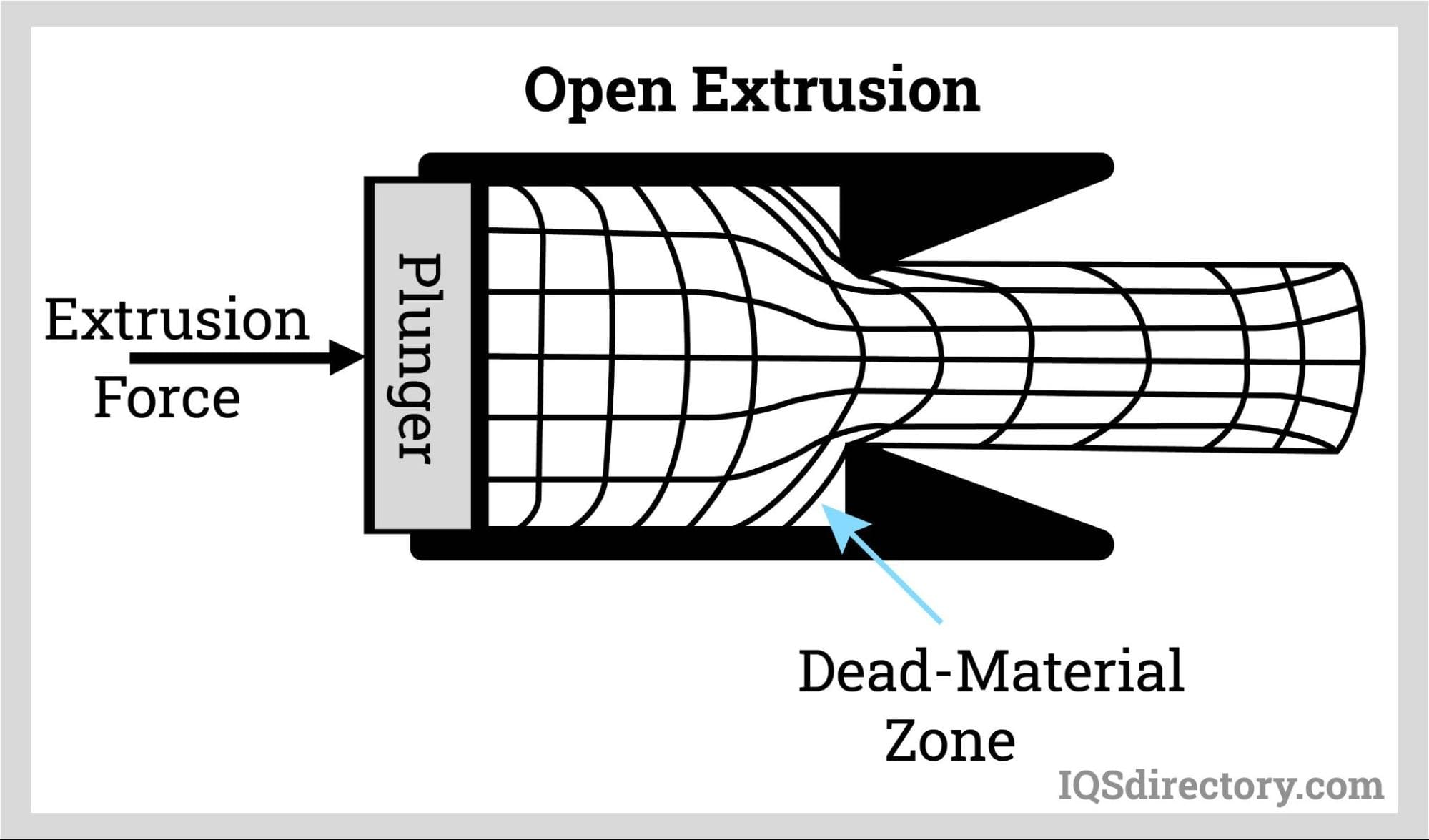
Недостатком, однако, является то, что для открытой экструзии требуется давление для прохождения детали через экструзионную часть инструмента. При слишком большом давлении из-за того, что деталь не поддерживается инструментами, произойдет деформация, приводящая к выходу из строя.
Экструзия с пленкой
Экструзия с захватом — полная противоположность процессу открытой экструзии. Это связано с тем, что деталь должна быть полностью помещена в инструмент, прежде чем ее пропустят через экструзионную часть инструмента. Это создает пространство для гораздо более сильного нажатия, чтобы уменьшить диаметр примерно на семьдесят пять процентов.
Ограничение заключается в том, что большая часть инструмента захватывается, чтобы частично освободить место перед выдавливанием, так что длина выдавливания получается короткой и более ограниченной, чем при открытом процессе выдавливания. Экструзию с захватом также называют замкнутой экструзией. Этот процесс отвечает за то, почему из жаток получаются сложные детали.
Радиальная экструзионная матрица часто предпочтительнее для замкнутого выдавливания деталей с холодной головкой. Это связано с тем, что такая форма матрицы снижает давление в матрице и улучшает характер течения проволоки при ее прохождении через матрицу. Практически во всех экструзионных штампах наилучшие результаты достигаются при изготовлении проволоки большего диаметра, чем готовый хвостовик.
Размер проволоки выбирается тщательно, чтобы размеры головки были примерно в два раза больше первоначального диаметра проволоки. Эта проволока также экструдируется до диаметра стержня и обжимается до размеров головки обычным способом.
Обратная экструзия
Процесс обратной экструзии определяется как основной процесс, используемый при изготовлении полых деталей, таких как втулки или гайки. При этом методе в деталь, находящуюся внутри матрицы, забивается штифт. На наружном диаметре штифта и стенках матрицы имеется значительный зазор. Это позволяет материалам течь в обратном направлении вверх вдоль штифта. Результатом этого является внешняя форма, которая начинает приобретать форму, и начало внутреннего канала или отверстия.
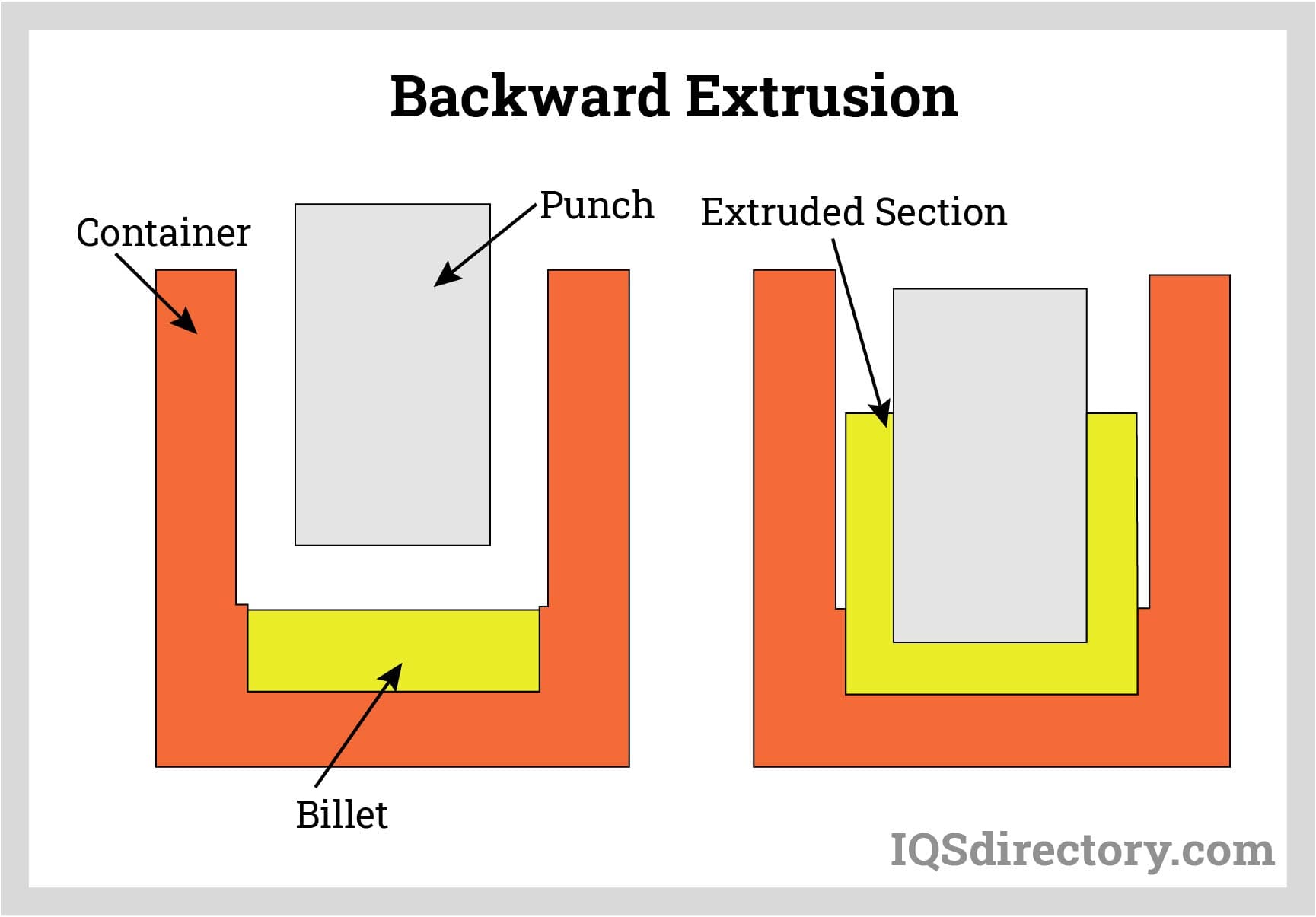
Процесс обратной экструзии также используется для изготовления внутренних приводных углублений во многих головках винтов. Последние процессы, которые можно выполнить при холодной высадке, — это обрезка и прошивка. Не все детали будут прокалываться или обрезаться; фактически, большинство винтов с наружной резьбой не должны проходить процесс обрезки.
Обрезка и прошивка — это одновременно процессы резки. Сила, конструкция и скорость инструментов позволяют срезать обрабатываемую область. Для деталей с наружной резьбой обрезка используется исключительно для придания формы хомута или головки, часто обрезной шестигранной головки. При изготовлении деталей с внутренней резьбой процесс обратного выдавливания обычно происходит со всех сторон детали. Заготовка будет содержать отверстия и не проходит полностью с двух сторон детали. Тонкая сетка материала разделяет отверстия.
Завершающим процессом является операция прошивки. Это когда в отверстие вводится штифт, который полностью срезает полотно и создает непрерывное отверстие в детали. В этих двух случаях, будь то внешняя часть, которая подвергается обрезке, или внутренняя часть, которая прокалывается, остается очень мало отходов. Это единственный металлолом, который используется в процессе холодной высадки, и он составляет очень небольшой процент от общего количества материала.
Глава 3: Применение и преимущества холодной высадки
В этой главе будут рассмотрены области применения и преимущества холодной высадки.
Применение холодной высадки
Процесс холодной высадки позволяет производить крепежные изделия с высокой эффективностью и хорошим качеством, экономя затраты и материалы. Однако для этого процесса требуется высококачественное сырье.
Для холодной высадки требуется определенный тип стали, используемой для изготовления крепежных деталей и соединений, называемый холоднокатаной сталью. Холодной высадкой также можно получать закаленные легированные стали, конструкционные стали и ферритно-мартенситные дуплексные стали.
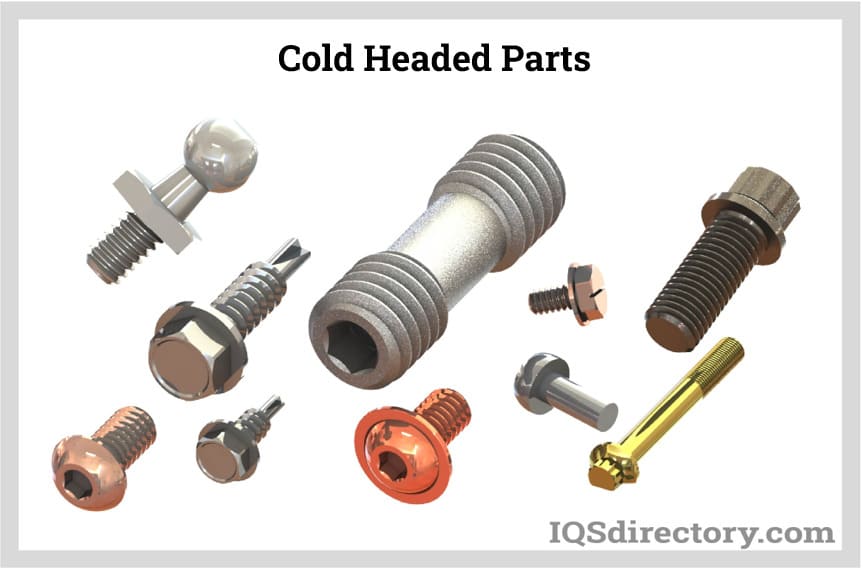
Преимущества холодной штамповки
Различные преимущества холодной штамповки включают:
Быстрое производство
Процесс холодной штамповки — это высокоскоростная операция; некоторые производители используют его для изготовления около 100 деталей в минуту. Скорость обеспечивает стабильное качество и точные результаты.
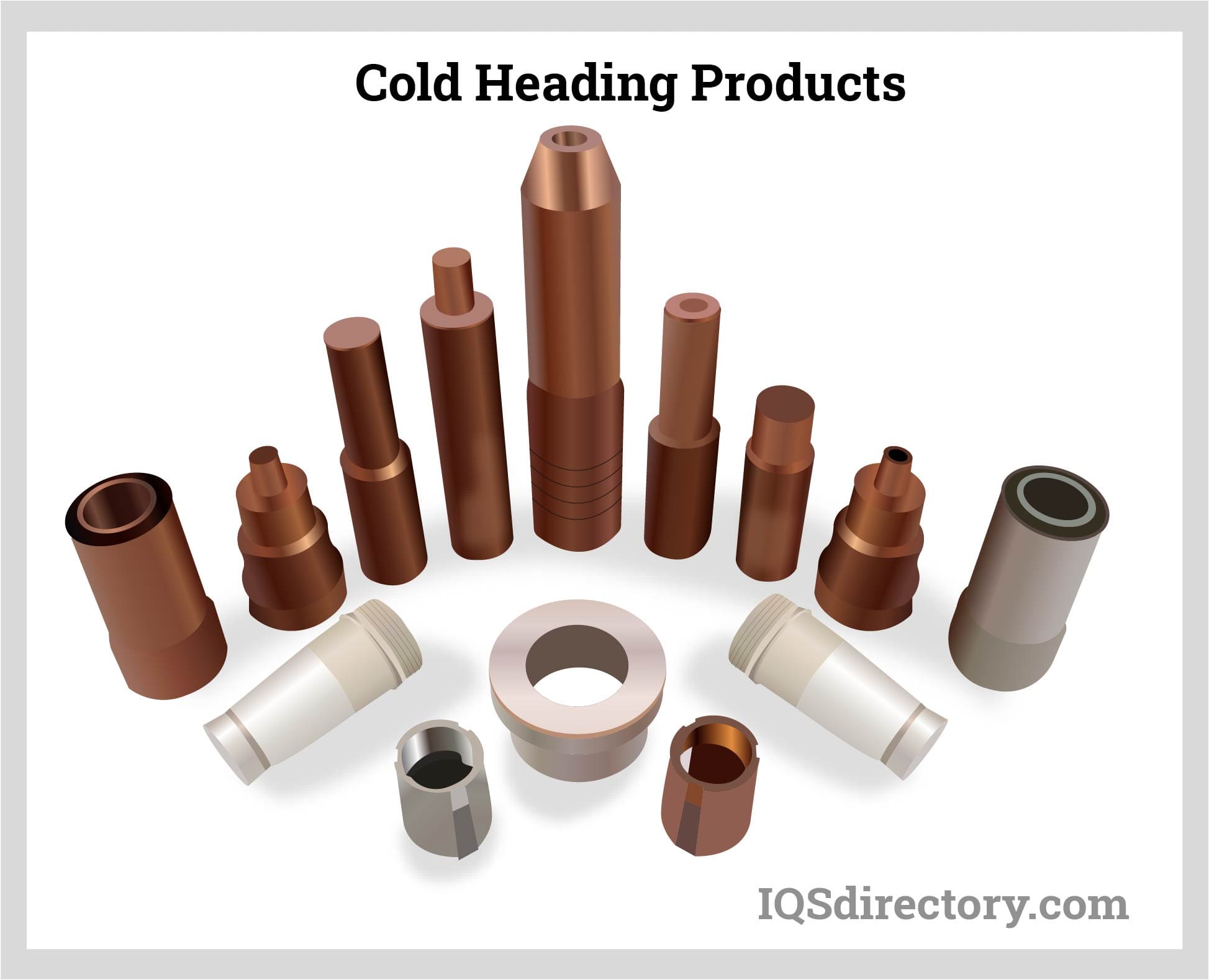
Повышенная прочность
Холодная штамповка придает детали прочность после холодного отверждения. Когда материал обрабатывается без резки или нагрева, он сохраняет свою первоначальную структуру. Зерна повторяют контуры детали, придавая ей дополнительную прочность.
Снижение энергопотребления
Процесс холодной штамповки не требует дополнительной энергии для нагрева материала для производства, в отличие от горячей ковки.
Недостатки холодной высадки
Некоторые из недостатков холодной высадки включают:
Ограничения по размерам
Чем больше диаметр крепежной детали, тем большее давление требуется для придания материалу требуемой формы. Очень большой станок может производить крепежные детали любого размера. Однако обычно это нецелесообразно, поскольку они больше подходят для процесса механической обработки.
Ограничения по материалу
Некоторые материалы лучше подходят для холодной штамповки, чем другие. Хотя можно использовать различные металлы, использование наиболее эффективных типов позволит создавать более качественные изделия.
Заключение
На протяжении многих лет процесс холодной высадки значительно способствовал совершенствованию технологии и получению более качественных результатов обработки. Таким образом, при выборе холодной высадки для конкретного процесса жизненно важно понимать его применение, преимущества и то, как работает каждый метод холодной высадки.